
Sonntag, August 06, 2006
FPGA Spartan-3

Samstag, April 29, 2006
Sensorneuheiten
Unser kleiner Bot nimmt mit der Zeit richtig Form und Gestalt an. Da er ja balancieren soll,
Danke schön
Samstag, April 08, 2006
Alu und Glas
Der nBot mit neuem Gesicht!!
Freitag, Februar 24, 2006
Display LCD-Modul Hyundai
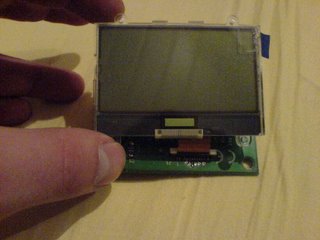
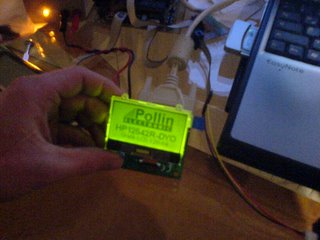

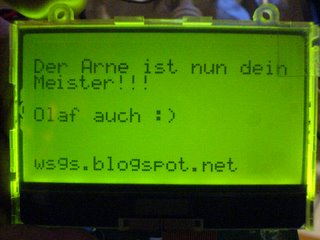
Freitag, Februar 10, 2006
Aluverarbeitung
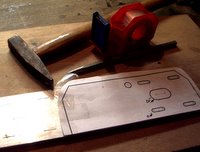
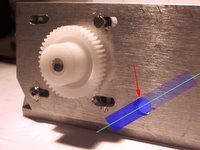
Das Holzmodell
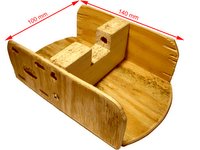
So beginnt die Suche nach den geeigneten Materialien und deren Beschaffung. Wir haben uns für Aluminium entschieden und sind unter www.alu-verkauf.de auf ein recht preisgünstiges und individuelles Angebot gestoßen.
Da ich aber noch eine alte 4mm Restplatte hatte, habe ich für die ersten Versuche diese verwendet. Die Lager beziehen wir von Igus©, die haben einen gut aufgeräumten und übersichtlichen Webauftritt, antworten schnell und freundlich auf Fragen und sind der offizielle Sponsor des RoboWorldCup 2006 in Bremen. Die restlichen mechanischen Teile haben wir über ebay ersteigert.
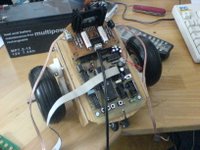
Modellbildung

In Autocad Inventor 6 (alte 30Tageversion, die bald abläuft :-( ) habe ich zunächst die gesamte Konstruktion gezeichnet und zusammengebaut.
Zuerst habe ich die Motoren nach einem Datenblatt nachgezeichnet, dann habe ich die Seitenwände und den Lagersteg(mittleres Aluteil) dimensioniert und als Bauteil erstellt. Die Reifen werden auf einer 6 mm Alu-Achse über ein Zahnrad vom Motor angetrieben. Dadurch wird das Lager der Motoren nicht beansprucht und eine längere Lebensdauer ist gewährleistet. Zudem ist das Übersetzungsverhältnis flexibler, da die Zahnräder (grün, Zeichnung unten) sich vertauschen lassen.
Zum Schluss habe ich den Deckel aus optischen Gründen aus Plexiglas gebaut und die nötigen Bohrungen und Gewinde für die Verschraubungen hinzugefügt.
Donnerstag, Februar 09, 2006
Display
Balancierender Roboter
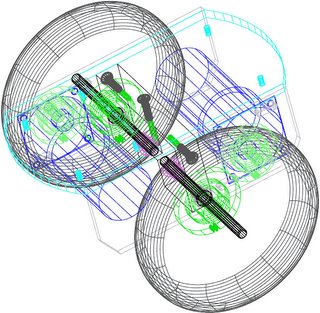
Mein erster Blogeintrag
Dies ist mein erster Blog und ich möchte hier ein Logbuch über die entstehung eines Roboters berichten. Ich werde wenn ich kann die ergebnisse meiner Arbeit hier herein stellen.
Abonnieren
Posts (Atom)